The industry associated with nuclear activity faces great challenges and challenges when innovating, designing and manufacturing large components for nuclear fusion.
To achieve this challenge, the Manufacture of large components with extremely complex geometries and excellent mechanical propertiescapable of resisting very high temperatures and radiation, which remains the key challenge for the development of this technology.
With the aim of overcoming these barriers, the project is born Rhodesan initiative that seeks to develop technologies of Advanced manufacturingespecially focused on the field of additive manufacturing combined with technologies such as hot isostatic pressed (Hip, Hot Isostatic Pressing), for the Critical component production For nuclear fusion reactors.
Promising energy solution
From the project drivers they are clear that «Nuclear fusion is presented as one of the most promising energy solutions For the future, thanks to your safety and the practically inexhaustible availability of resources ».
This project, with a duration of four years, «intends to provide knowledge and technology companies, which allows them face future projects in the field of nuclear fusion in Spain»They add.
Rodas has budgeted 7.78 million euros to reach this purpose with public financing of 5.54 million euros Once Ministry of Science, Innovation and Universities through the Center for Technological Development and Innovation (CDTI) and the State Research Agency (AEI), within the framework of the Transmissions 2024.
The objective is to help solve the current challenges that exist to obtain the components of nuclear fusion reactors. Among them are How to face long delivery deadlinesthe Complex manufacturing processes that involve many successive stages of mechanized, unions and thermal treatments, as well as High consumption of raw materials and energy.
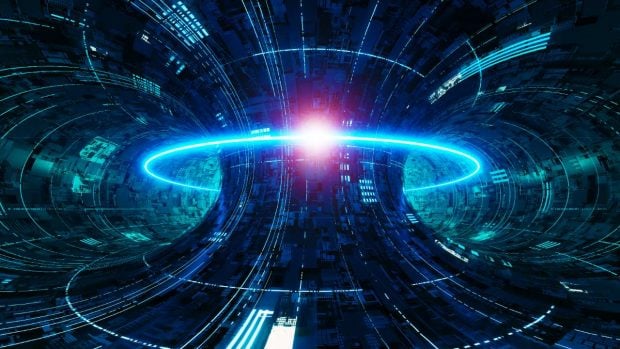
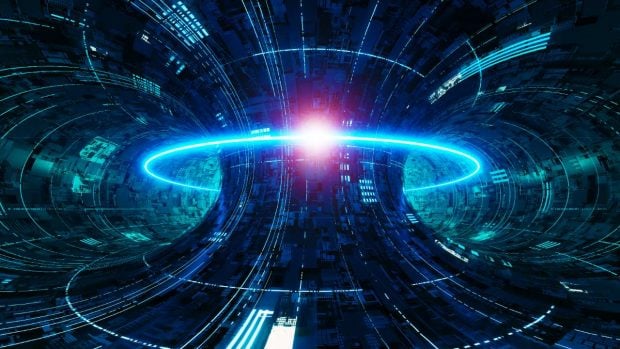
Innovation in materials, manufacturing technologies and essays
The project is articulated around three key areas: Manufacturing materials and technologies and advanced tests. “With the results obtained, companies will be trained in knowledge and technology to address future projects and tenders related to nuclear fusion,” says Nerea Ordás, CEIT’s additive manufacturing director.
In the field of advanced materials, and here the specialized jargon of the sector appears, «we will work on the development of new polvimetallurgical alloys, such as Eurofer and Cucrzr, capable of supporting high temperatures and radiation».
In addition, they point out that it will optimize The gas atomization process to improve the production of metal powders employees in additive manufacturing, thus facilitating their integration into industrial processes.
New high performance alloys
In this sense, we will work on research and development of new alloys of high performance materials and advanced thermomechanical properties specially designed for nuclear fusion components.
The objective is to demonstrate that «additive manufacturing technology is technically and economically viable for obtain actively refrigerated componentsof complex geometry and large dimensions, capable of complying with the strict requirements of the nuclear fusion, ”says Marcos Pérez, director of business development at Leading Metalmechanical Solutions.
Regarding advanced manufacturing, different manufacturing techniques will be investigated from dust or metallic thread, such as PBF-L (direct fusion of laser metal), DED (Focharged energy deposition), Waam (additive manufacturing by arc and thread) or the novel ROV-MAM technique, with the aim of orBTain pieces with complex and large geometries and obtaining a significant reduction in the waste of material. In addition, manufacturing processes hybridization will also be investigated.
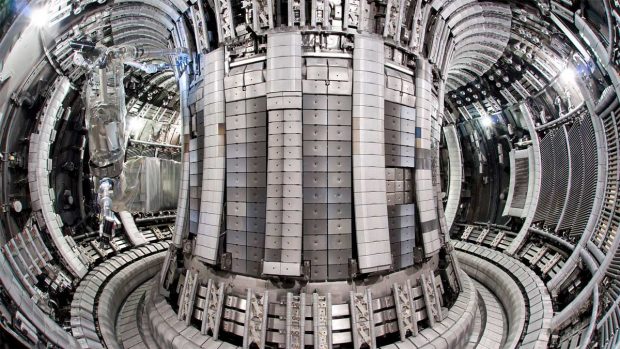
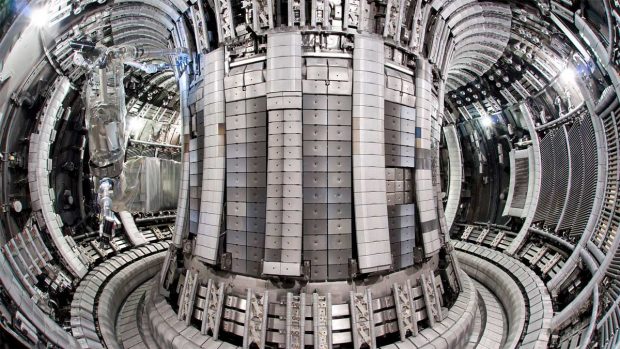
Hot isostatic pressed
One of the main innovations of the Rodas project will be the possibility of Simultaneous application of thermal treatments and hot isostatic pressed technology (Hip, hot isostatic pressing) developed by Hiperbaric.
«We are developing a new press generation and large hip oven, unique in Spain, with high cooling speeds and equipped with an advanced control architecture through the application of artificial intelligence»Indicates Andrés Hernando, CEO of Hiperbaric.
Finally, advanced tests will be carried out to validate new materials and processes through non -destructive techniques, such as tomography computerized and ultrasoundthus ensuring the integrity of the components without the need for destructive tests.
Materials reduction
The development of these technologies It will have a significant impact on industry, science and sustainabilitycontributing to the development of nuclear fusion as a source of energy.
Thanks to the optimization of advanced manufacturing processes, It is expected to reduce the production times of key components from eight to two weeks and minimize the waste of material by up to 80%respecting the environment. In addition, the use of new materials will allow Improve the duration and efficiency of fusion reactors.
Spanish industrial fabric effect effect
A tractor effect of Spanish industrial fabric will be generated, promoting companies training in thematic areas related to materials with advanced properties and allowing these companys position in the science industry sector.
It will also facilitate the access to public tenders of ifmif-dones (international installation of irradiation of fusion materials-source of demo demo neutrons) or iter (international experimental thermonuclear reactor).
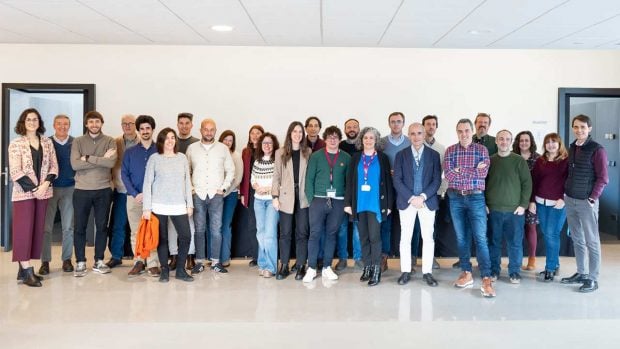
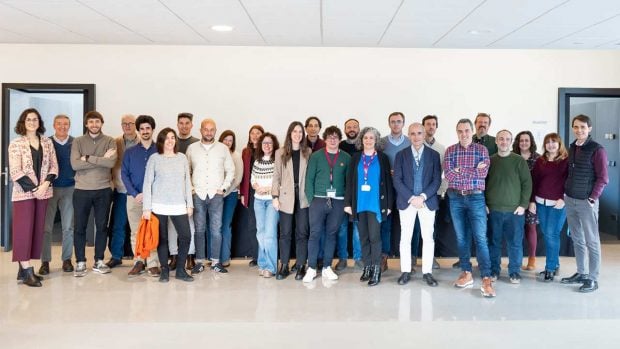
Reference consortium for an ambitious project
The Rodas project has a Consortium formed by two groups. On the one hand, the grouping of the Center for Technological Development and Innovation CDTI, led by Leading Metalmechanical Solutions and composed of the companies Hiperbaric, Rovalma, Innomaq21 and Novadep NDT Systems.
On the other hand, the grouping of the State Research Agency (AEI), headed by the CEIT Technology Center Association and formed by CIEMAT, Idonial Foundation and the University of Granada.
While the AEI group will assume research, material development, manufacturing processes optimization And the validation of components, the CDTI group will focus on the VAlidation of advanced manufacturing technologies and real -scale applications development.
Research and experience
This combination of research and industrial practical experience guarantees the viability and success of the project, allowing the effective transfer of the scientific advances to industry.
The project was launched last January with A meeting held at the CEIT facilitiesin which all the members of the consortium participated. During the meeting the first steps were defined and the road map was established for the next few years.
Initiative of the University of Navarra
CEIT is an integrated technological center in the Basque Research and Technology Alliance (BTA), and created in 1982 at the initiative of the University of Navarra. As a private non -profit organization, its mission is Improve the competitiveness of companies through the generation and transfer of knowledge in the field of applied research.
With a strong industry orientation, CEIT works in close collaboration with companies from various sectors to develop innovative technological solutions that respond to their strategic needs. Its specialization is articulated around three major areas: advanced manufacturing, sustainable mobility and circular economy.
Participating companies
Leading is a SME constituted in 1972 and focused on design, Development and manufacture of precision mechanized and weldsprototypes, short-media serial production of components, as well as tools and models, in a wide range of materials, both ferric and non-ferric, and in all kinds of productive forms.
The main business of this company is, therefore, machining and precision welding; The delivery of complex mechanical sets, offering the possibility of complete processes management by supplying hand key projects.
It focuses on get the best design solution To improve product performance based on the initial specifications and requirements of the customer, working closely with each customer, delivering the finished product with all the required certifications.
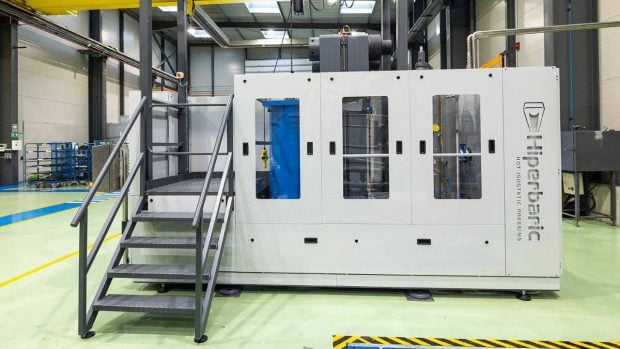
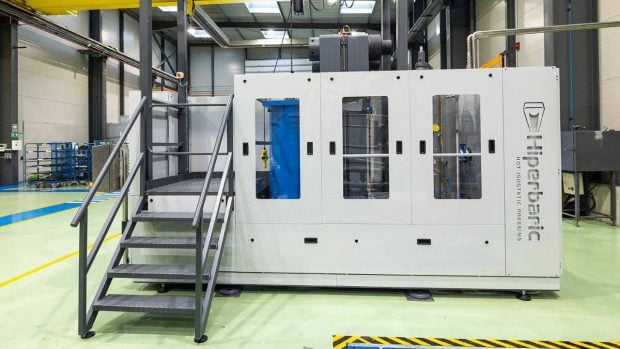
High pressures
Hiperbaric is a bourgeois company dedicated, since 1999, to the design, manufacture and marketing of high -pressure technology and industrial equipment. For more than two decades It is machinery supplier for high pressures (High Pressure Processing, HPP) applied to the food sector, in which it is world leader with more than 65% of the market share.
In 2019, it opened a new business line focused on design and development industrial equipment for hot isostatic pressing (Hot isostatic Pressing, Hip).
In 2021 It launches another innovative business line: hydrogen compression technology (H2) At very high pressure, from renewable energy, to participate in the challenge of sustainable mobility and decarbonization of the industry. In 2024 the company celebrated its 25th anniversary.